Knife Edge Sharpening, It's All About the Angles
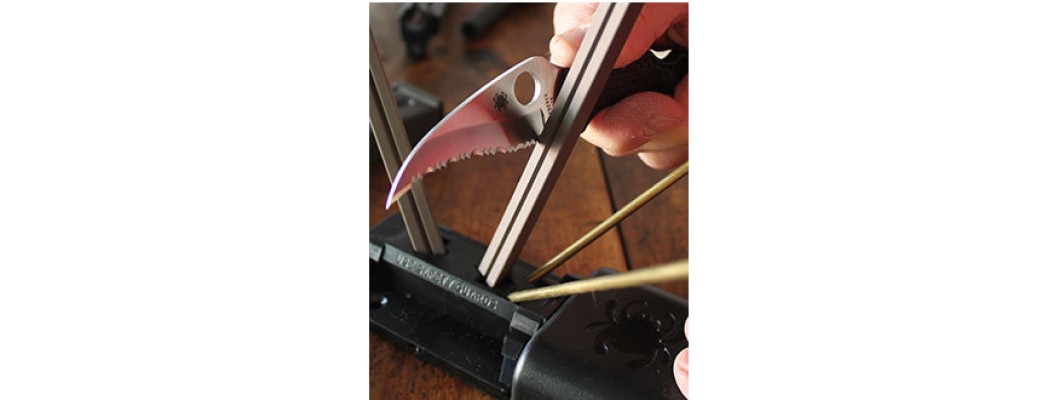
One thing I've learned working with hardcore trades people is that keeping tools in tip top shape is critical. Nowhere is this more true than when it comes to professional knives - and I don't mean the ones used in a kitchen! When it comes to knives you better have a nice sharp edge on the blade if you expect to get the job done. Do you know how to sharpen a knife? Edge sharpening is not as simple as you might think. But, it is absolutely necessary to maintaining the value and safety of your knife.
When it comes to knives and sharpening knives look no further than Spyderco. Since 1976 Sal and Gail Glesser have focused on sharp knives. In the beginning, they made their living by focusing on sharpening edges. It was during these early years that Sal learned the best way to set an edge on a blade. In 1978 Sal invented the Tri-Angle Sharpmaker™.
To say the Tri-Angle Sharpmaker™ was revolutionary may be an understatement. What isn't an understatement is the impact of angles on creating an edge that will do the job you need your knife to do.
At this point, I have to admit that my high school geometry just isn't up to the task of explaining all the reasons why simply using a flat whetstone to set the edge won't get the job done. Even so, it is useful, and interesting, to learn more about how to sharpen an edge and why getting the proper angle for that particular type of nice is so important.
To better understand all the "angles" involved, we've included an excerpt from a recent Spyderco byte blog post. If you get this all figured out give me a call, maybe you can explain it to me!
Thank you Spyderco, here's to getting the angles right...
------------------------------------------------------------------------------------------------------
Understanding All The Angles(Story extracted from July edition of Syperco bytes)The term “edge geometry” is one we hear a lot when discussing the cutting performance of knives. Although the geometry of the terminal cutting edge of a blade is certainly important, understanding real cutting performance means looking at “all the angles.” ![]() To give the edge greater strength and make the blade easier to produce, the bevels typically don’t converge completely. Instead, they leave a thicker section of steel near the edge. A narrow secondary bevel is then ground at a steeper angle to create the actual cutting edge. The terminal thickness of the steel adjacent to the cutting edge is also a determining factor in the overall edge geometry of the blade.
A full-flat grind with a thin terminal edge thickness creates a very acute angle near the edge and the long, gradual rise of the bevels. This geometry parts the material being cut with minimal friction and offers excellent cutting performance. It also produces a distal taper that reduces the weight of the blade, but also decreases its strength.
![]() In many ways, a hollow grind offers the best of both worlds. Since its bevels are actually concave, it can produce a very thin terminal edge thickness and support an acute cutting edge angle, while still maintaining a thick spine for strength. Hollow-ground blades can also be sharpened many times before the edge wears into the thicker part of the steel. Flat-ground and saber-ground blades reach that point sooner and ultimately must be sharpened at a more obtuse angle.
![]() Spyderco takes all of these factors into consideration when we produce our knives to ensure that every blade offers the best possible cutting performance within the scope of its design, blade material, and intended use. When it comes to edge geometry, we really do work all the angles. Learn More
------------------------------------------------------------------------------------------------------Did you read the whole article? That's amazing. If you've got the whole angle thing figured out maybe you can give me a call and explain it. Either that or I'm going to have to go back to high school geometry and try to refresh my skills. Thanks for stopping by our blog, if you're looking for Spyderco products just click here. |